Beyond DMAIC : Exploring Other Six Sigma Methodologies and Extensions
- arunrtb
- Mar 14, 2024
- 8 min read
Updated: Oct 3, 2024

Six Sigma, the data-driven methodology designed to improve processes by optimizing variations and reducing defects, has become a cornerstone of quality management in various industries. While the DMAIC (Define, Measure, Analyse, Improve, and Control) framework is widely recognized, there's more to Six Sigma than this foundational approach. In this comprehensive guide, we'll delve into the world of Six Sigma to explore other methodologies and extensions that provide valuable tools for quality improvement. These alternative Six Sigma pathways open up new avenues for businesses and organizations seeking to enhance their processes and drive efficiency. So, let's embark on this journey beyond DMAIC and discover the rich landscape of Six Sigma methodologies.

1. DMADV: A Journey to Perfection
DMADV, or Define, Measure, Analyse, Design, Verify, is an alternative Six Sigma methodology that focuses on creating entirely new processes or products with the ultimate goal of achieving perfection. Unlike DMAIC, which aims to improve existing processes, DMADV is a pathway to innovation and ground-breaking quality.
In the DMADV approach, organizations start from scratch, defining the critical elements of a new process or product. They meticulously measure and analyse each component, seeking to understand customer requirements in depth. The design phase involves crafting a solution that not only meets these requirements but also strives for excellence, setting a high bar for efficiency and quality. Finally, the verification stage ensures that the new process or product performs as intended, meeting the standards of perfection set at the beginning.
DMADV is particularly valuable in situations where organizations are introducing entirely new innovations or striving to enhance the quality of novel offerings. It provides a structured framework for creative problem-solving and achieving unparalleled levels of excellence.
2. Lean Six Sigma: Combining Efficiency and Quality
Lean Six Sigma is a hybrid methodology that merges the principles of Lean manufacturing with Six Sigma quality management. It is a powerful approach that aims to balance efficiency and quality, making it particularly effective in improving processes in various industries.
Lean principles, borrowed from the Toyota Production System, emphasize eliminating waste, streamlining operations, and enhancing efficiency. They focus on speed, cost reduction, and maximizing value. In contrast, Six Sigma targets defect reduction, process improvement, and quality enhancement. It emphasizes a data-driven approach and structured problem-solving.
When Lean and Six Sigma are combined, organizations achieve a synergy that addresses both speed and quality. Lean tools, such as 5S, Kanban, and Value Stream Mapping, can be seamlessly integrated into Six Sigma projects. This synergy results in improved efficiency, reduced waste, and enhanced quality. Lean Six Sigma is particularly effective in manufacturing and service industries, offering a holistic approach to process optimization that balances cost savings with customer satisfaction.
3. DFSS: Design for Six Sigma
DFSS, or Design for Six Sigma, is a Six Sigma methodology that focuses on designing new processes or products with the highest quality standards right from the outset. It is a proactive approach that places a strong emphasis on understanding customer requirements and designing solutions that not only meet but often exceed those expectations.
In DFSS, organizations start by defining the critical parameters and requirements for a new product or process. This phase involves a thorough understanding of customer needs, preferences, and expectations. The next step is to measure and analyze the design elements to ensure that they align with these requirements. Once the analysis is complete, the design phase involves creating a solution that is poised to deliver exceptional quality and performance.
DFSS is particularly valuable in industries where innovation and product development are central to success. It helps organizations develop products or processes that are highly competitive, have fewer defects, and meet or exceed customer expectations right from the start. This methodology promotes a culture of excellence and innovation, making it a valuable addition to the Six Sigma toolkit.
4. Lean: Streamlining and Speed
Lean, often associated with the Toyota Production System, is a methodology that focuses on streamlining processes to achieve optimal efficiency and speed. While Lean is not exclusive to Six Sigma, it can be seamlessly integrated into Six Sigma projects to drive process improvements.
The core principles of Lean revolve around reducing waste, enhancing flow, and increasing speed. Lean tools such as 5S, Kanban, Value Stream Mapping, and JIT (Just-in-Time) production are used to eliminate inefficiencies and optimize workflow.
The 5S methodology emphasizes sorting, setting in order, systematic cleaning, standardizing, and sustaining a workspace, making it more organized and efficient. Kanban is a visual scheduling system that helps manage inventory and production processes. Value Stream Mapping identifies and eliminates non-value-added activities in processes, creating a smoother flow. JIT aims to reduce excess inventory and only produce what is needed when it is needed.
When integrated with Six Sigma, Lean principles contribute to achieving streamlined processes, faster cycle times, and reduced operational costs. The combination of Lean's focus on efficiency and Six Sigma's emphasis on quality creates a holistic approach that optimizes operations, ultimately leading to better customer satisfaction and a competitive edge.
5. TOC: Theory of Constraints
The Theory of Constraints (TOC) is a management philosophy and methodology that focuses on identifying and alleviating bottlenecks or constraints within a system to improve overall efficiency and productivity. Developed by Dr. Eliyahu Goldratt, TOC is widely used in various industries to optimize processes, increase throughput, and maximize profitability.
At its core, TOC operates on the principle that any system, whether it's a manufacturing process, a supply chain, or a project, has at least one constraint that limits its performance. These constraints can impede the achievement of organizational goals. TOC aims to identify these constraints, prioritize them, and develop strategies to alleviate or eliminate them.
TOC offers a five-step process to address constraints:

Identify the Constraint: The first step is to pinpoint the bottleneck that is limiting the system's overall performance. This can be done through data analysis and observation.
Exploit the Constraint: Once identified, the constraint is maximized in its utilization to make the best use of existing resources.
Subordinate Everything Else: Other parts of the system are adjusted to support and synchronize with the constraint, ensuring that they don't overload or create conflicts with the bottleneck.
Elevate the Constraint: Efforts are made to increase the capacity of the constraint, whether through additional resources, process improvements, or technology enhancements.
Repeat the Process: As constraints are addressed and alleviated, new constraints may emerge. The TOC process is ongoing, continuously identifying and addressing constraints to improve the system's performance.
.
6. TRIZ: Innovation Through Creativity
TRIZ, or the Theory of Inventive Problem Solving, is a problem-solving and innovation methodology that originated in Russia. It provides a structured approach to solving complex problems and fostering innovation by leveraging creative thinking and systematic analysis.
TRIZ is founded on several principles, including the concept that inventive solutions to problems are not arbitrary but follow identifiable patterns. It introduces inventive principles and inventive standards, which serve as a set of strategies and guidelines for tackling problems. The methodology also includes tools such as the 40 inventive principles, the 76 standard solutions, and the analysis of contradictions to guide problem-solving.
One of TRIZ's fundamental concepts is the Ideal Final Result (IFR), which represents the perfect solution to a problem. TRIZ practitioners aim to work towards this IFR through incremental improvements and innovative thinking.
TRIZ can be a valuable addition to Six Sigma methodologies as it encourages creative problem-solving and can help organizations find breakthrough solutions to complex issues. It complements Six Sigma's data-driven and process improvement focus by bringing a different perspective to the innovation process, making it a powerful tool for fostering creativity and continuous improvement.
7. Integration of Six Sigma and Agile
The integration of Six Sigma and Agile methodologies represents a dynamic approach to process improvement and project management, combining the structured, data-driven principles of Six Sigma with the flexibility and adaptability of Agile.
Six Sigma is known for its focus on reducing defects, improving process efficiency, and enhancing quality. It follows a structured approach, often referred to as DMAIC (Define, Measure, Analyze, Improve, Control), to identify, analyze, and eliminate process variations. Six Sigma projects are typically sequential and rely on well-defined processes.
Agile, on the other hand, is a project management approach often used in software development and other creative industries. Agile emphasizes collaboration, adaptability, and customer feedback. Agile projects are executed in short iterations, or sprints, where requirements can evolve as the project progresses.
The integration of Six Sigma and Agile brings the best of both worlds. It combines the robust problem-solving capabilities of Six Sigma with the agility and customer focus of Agile. This integration can offer several advantages:
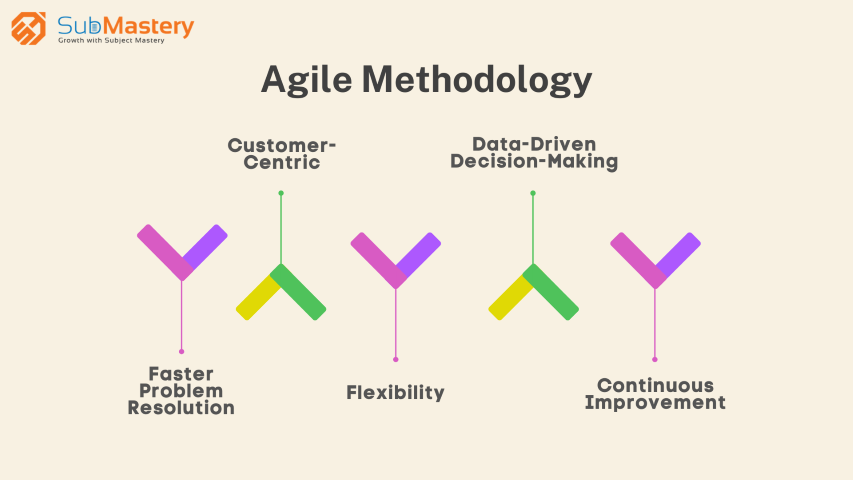
Faster Problem Resolution: Agile's iterative approach can accelerate the identification and resolution of issues, ensuring that problems are addressed promptly.
Customer-Centric: Agile's focus on customer collaboration aligns well with Six Sigma's emphasis on meeting customer requirements.
Flexibility: Agile allows for changing requirements, which can be essential in dynamic environments.
Data-Driven Decision-Making: Six Sigma's data analysis complements Agile by providing a solid foundation for decision-making.
Continuous Improvement: Six Sigma's DMAIC framework can be applied to Agile projects, ensuring that each iteration becomes an opportunity for process improvement.
.
8. Healthcare-Specific Six Sigma Methodologies
The application of Six Sigma in healthcare has led to the development of specialized methodologies tailored to the unique challenges and needs of the healthcare industry. These methodologies focus on improving patient care, reducing medical errors, and enhancing operational efficiency. Here are some healthcare-specific Six Sigma methodologies:
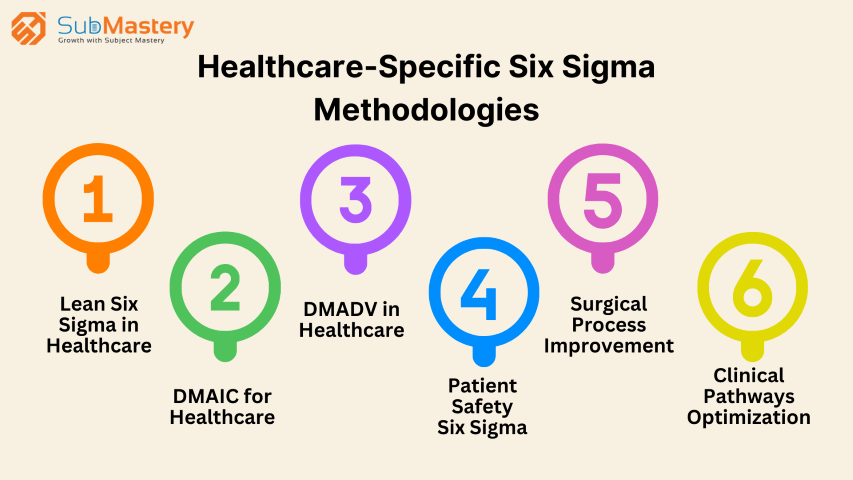
Lean Six Sigma in Healthcare: This combines Lean principles with Six Sigma methodologies to streamline healthcare processes. It aims to eliminate waste, reduce waiting times, and improve overall patient care. Lean Six Sigma is widely used to enhance efficiency in healthcare operations, such as hospital admissions, emergency department processes, and laboratory services.
DMAIC for Healthcare: DMAIC (Define, Measure, Analyze, Improve, Control) is a versatile Six Sigma methodology that can be adapted for healthcare settings. It helps identify and rectify problems in patient care, administrative processes, and resource management. DMAIC is applied to areas such as reducing patient wait times, improving medication administration, and enhancing the accuracy of medical records.
DMADV in Healthcare: While DMADV (Define, Measure, Analyze, Design, Verify) is traditionally used for designing new products and processes, it can also be beneficial in healthcare. Hospitals and healthcare providers use DMADV to design new healthcare processes, ensuring they meet patient needs, enhance efficiency, and maintain the highest standards of care.
Patient Safety Six Sigma: This methodology places a strong emphasis on reducing medical errors and improving patient safety. It involves using Six Sigma tools to identify and mitigate risks in healthcare procedures, medication administration, and patient handling.
Surgical Process Improvement: In surgical settings, Six Sigma methodologies can be applied to improve the quality and safety of procedures. This involves optimizing surgical processes, reducing complications, and enhancing patient outcomes.
Clinical Pathways Optimization: Clinical pathways are standardized protocols for patient care. Six Sigma is used to evaluate and optimize these pathways to ensure that they deliver the best care efficiently.
These healthcare-specific Six Sigma methodologies are critical for enhancing patient care, minimizing errors, and increasing operational efficiency in healthcare organizations. They offer structured and data-driven approaches to address the unique challenges that the healthcare industry faces, ultimately improving the quality of healthcare services provided to patients.
Conclusion
While DMAIC is the bedrock of Six Sigma, these alternative methodologies and extensions offer a diverse set of tools to cater to various industries and organizational needs. The choice of methodology depends on the specific objectives and challenges a business or organization faces. The world of Six Sigma is vast, and as organizations strive for continuous improvement, they can explore these additional paths to optimize processes, enhance quality, and ultimately achieve excellence. Beyond DMAIC lies a realm of opportunities for those seeking to elevate their quality management efforts.
Comments